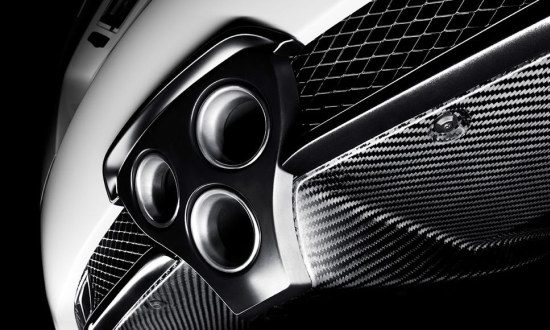
Koolstofvezel neemt een steeds belangrijkere plaats in in de autoindustrie, maar wat is het precies, en wat is het onderscheid tussen de gebruikte soorten carbon fibre reinforced plastic (CFRP)? Hierop geven we in dit artikel een antwoord.
In de basis is carbon het volgende: een polymeer/plastic die een versterkt met vezels, dat met behulp van een speciale hars in een vacuumzak onder hoge druk in een speciale oven ‘gebakken’ wordt. Het materiaal is licht en supersterk. In deze combinatie heeft elk materiaal zijn eigen functie, de vezels dragen de belasting, het plastic beschermt de vezel en verbindt ze.
Carbon fibre reinforced plastic (CFRP) is een composiet: letterlijk een samenstelling van 2 materialen waardoor de gemengde eigenschappen beter zijn dan de basis.
Omdat de verwerking van koolstofvezel bijna altijd met de hand gebeurt, is het een duur materiaal. BMW is de eerste massaproducent die (via zijn dochter SGL Carbon) koolstofvezel machinaal en op grote schaal weet toe te passen, in de monocoque van de BMW i3, die door zijn stijfheid geen B-stijl meer nodig heeft.
Naast BMW zijn de toepassingen van carbon vooral high-end, supercars van Lamborghini en Ferrari bestaan voor een flink deel uit carbon, en ook in de racerij wordt het lichte materiaal veel toegepast. Wie een auto van onder de 100.000 euro met carbon monocoque wil, maar geen BMW, is aangewezen op de Alfa-Romeo 4C, die zijn vezels krijgt aangeleverd van het Nederlandse Ten Cate. Of deze McLaren, maar die heeft slechts 2 wielen.
Koenigsegg, tot slot, bakt zijn eigen kleine koolstofvezel onderdelen, bijvoorbeeld de (holle) velgen voor de Agera.
Verschillen in sterkte
Vanzelfsprekend is niet elk stukje koolstofvezel even sterk. Producenten hebben op bepaalde strategische plekken extra stevigheid nodig, hiervoor wordt carbon gebruikt dat is opgebouwd uit meerdere lagen. Het spreekt voor zich at dit duurder (en zwaarder) is dan een weefsel met minder lagen, maar dat is een keuze die gemaakt wordt. De LaFerrari bijvoorbeeld kent 4 verschillende soorten carbon van verschillende sterkte.
Behalve een praktische gewichtsbespaarder is carbon ook niet te onderschatten als PR-tool. Het zal niet de eerste keer zijn dat een fabrikant zich triomfantelijk op de borst klopt dat zijn carbon veel stijver is dan dat van de concurrentie.
Feit is wel dat het materiaal zich, naast de tradionele luchtvaart- en racesector, de laatste jaren op een toenemende aandacht van de automotive industrie kan verheugen. Lamborghini richtte enkele jaren geleden een Carbon Research Facility op.
Droge vs natte composieten
Koolstofvezel laat zich onderverdelen in droog en nat carbon. De droge variant is ook wel bekend als prepeg. De rol waarop het basismateriaal zit is al geïmpregneerd met de epoxyhars. Het is stug materiaal, maar zodra je het vacumeert en in de oven stopt zal het materiaal zich gaan vormen, omdat de hars vloeibaar wordt.
Droog carbon is de crème-de-la-crème onder de koolstofvezels, met een fabricageproces dat een foutmarge van nagenoeg nul kent. Het materiaal is tot 70% lichter dan nat koolstofvezel en bevat volstrekt geen overtollige hars. Het andere nadeel (naast zero-tolerance) laat zich raden: het goedje is peperduur. Onderstaande grafiek toont echter dat als je sterk wilt, je aangewezen bent op prepeg (de andere 2 methoden zijn Resin Transfer Molding (RTM) en Sheet Molding Compound (SMC)):
Bij nat koolstofvezel wordt het koolstofvezel geweven in een mal, en aan de oppervlakte voorzien van een harslaag. In de oven wordt de hars onder een vacuum door de koolstofvezels geduwd om zo de verbinding die het goedje zo sterk maakt tot stand te brengen. Mits goed uitgevoerd komt er een eindproduct uit de oven met een gelijkmatig verdeelde hoeveelheid hars, dat over de hele oppervlakte ongeveer even sterk is.
Bovenstaande methode wordt in de vakterminologie ook wel ‘infusion‘ genoemd. Mocht het doel van de koolstofvezeltoepassing meer cosmetisch dan praktisch zijn, dan kan een goedkopere methode worden toegepast die ‘painting’ heet. Hierbij wordt de vacuumoven overgeslagen. Het eindproduct is dan stukken goedkoper, maar mist tegelijkertijd consistentie en is bovendien zwaarder.
In het geval van bijvoorbeeld een paar carbon sierstrips in het interieur van je Audi S8 is dat echter geen ramp, want die strips gaan je leven niet redden bij een crash.
Hoe onderscheid ik droog van nat carbon?
Dat is niet heel moeilijk, de twee verschillen behoorlijk in uiterlijk, waarbij de naam al voldoende uitleg geeft. Droog oogt doffer, en nat glanst meer. Kijk maar naar onderstaande foto.
Update: naar het schijnt is het herkennen van de soorten een stuk lastiger dan aanvankelijk beschreven: de malkwaliteit bpaalt de ‘dofheid’ van CFRP. Vooral leidend in het onderscheid is de verhouding tussen koolstof en hars.
Een technische benadering van CFRP
Nu we de verschillende varianten hebben gedefinieërd wordt het tijd een professional aan het woord te laten. Een van onze lezers, Jordy van Nimwegen, is werkzaam in de industrie, en deelde de volgende kennis met ons:
Grofweg worden er bij CFRP 2 varianten toegepast: georiënteerd, waarbij de vezels in een vooraf bepaalde richting worden toegepast (deze hebben de beste eigenschappen) en ongeoriënteerd, waarbij de vezels in allerlei richtingen liggen. De tweede groep wordt al lange tijd en veelvuldig toegepast in auto’s, bijv. in bumpers en interieurdelen:
- Waarom is de oriëntatie zo belangrijk?
Je kan de vezel zien als een touw in gebed in plastic, onder o graden trek je volledig aan de vezel echter als je doordraait naar 90 graden worden de vezels alleen nog bij elkaar gehouden door het plastic. Door de vezels in richting van de belasting te plaatsen kun je optimaal gebruik maken de eigenschappen, dit wordt anisotropie genoemd. Metalen en plastics hebben gelijke eigenschappen in alle richtingen en zijn dus isotroop.
- Waarom is het zo interessant?
Gewicht, zoals bekend, is een killer voor acceleratie, handling en uiteindelijk verbruik. Materialen worden mechanisch globaal gedefinieerd door hun stijfheid en sterkte. Echter is de dichtheid ook van groot belang.
- Prijzig
Koolstofvezel wordt geproduceerd door een plastic vezel te ‘verkolen’ via een serie ovens. Dit proces vergt een hoge mate van nauwkeurigheid, te weinig verkolen en de eigenschappen blijven dichtbij de basis plastic vezel, te ver verkolen en de vezel wordt bros en fragiel. Hierdoor ligt de prijs van koolstofvezel tussen de 15-25€/kg, in vergelijking de staalprijs ligt op enkele euro’s per kg.
De daarop volgende stap, het samen brengen met plastic van het CFRP-deel is in vele manieren mogelijk. Als we kijken naar de voor de automotive geschikte productietechnieken dan worden onderdelen opgebouwd door lagen vezels, al dan niet in een weefsel, op elkaar te stapelen in een mal. Daarna wordt de mal gesloten en het plastic in vloeibare vorm ingebracht. Het om zetten van een vloeibaar plastic naar een vast plastic kan op kamertemperatuur maar voor snelheid en kwaliteit is het gebruikelijk om de temperatuur te verhogen tot 80-150graden.
- Is het nou echt een wondermateriaal?
Ja en nee. Het is licht en kan tevens in voor metaal onmogelijke vormen gemaakt worden, maar er kleven ook nadelen aan: CFRP’s hebben een heel ander faalgedrag dan metalen, deze buigen en vervormen voordat ze kapot gaan, CFRP’s daarentegen breken meteen.
Verder is de gebruikstemperatuur direct afhankelijk van het gebruikte plastic, die vaak niet veel hoger dan 150°C toegepast kunnen worden. Ook is het verbinden niet mogelijk volgens het conventionele lassen, verlijmen is een veelgebruikte techniek; hierin heeft de luchtvaart al een ruime ervaring.
Leesvoer
Nog meer weten? Dan bevelen we je deze serie van The Truth About Cars aan, dat in 2012 bij Lexus op bezoek ging, en keek hoe de LFA geproduceerd wordt.
Ga zo door! Dergelijke artikelen vind ik altijd erg interessant.
Super interessant artikel jongens!
Mooi! Eindelijk weer een technisch verhaal met inhoud! Mogen er meer van langskomen.
Lekker stukje leesvoer!
Ik ga eerst even eten en dan lezen. Reuze interessant!
Het herkennen van droog en nat koolstofvezelcomposiet is alleen op destructieve wijze te onderscheiden. Simpelweg omdat men vaak een clearcoat aanbrengt op beide composieten. (Het hoeft niet altijdzo te zijn, zo heeft de McLaren P1 geen clearcoat op de CF-onderdelen in het interieur wegens gewichtsbesparing.) Dus visueel onderscheiden is vrijwel onmogelijk. Overigens worden de onderdelen niet gebakken in een oven maar in een autoclaaf. Een autoclaaf is niets anders dan een compressieoven. Men gebruikt steeds vaker aramidevezels (kevlar) i.c.m. koolstofvezels om een composiet te verkrijgen met voorspelbare defect indicatie. Verder een goed artikel hoor. (^^,)
@AutomotiveDesigner: zeer interessant. En wat doet men dan in geval van defect indicatie? Ik ben wel benieuwd naar de aangehaalde repareer technieken in het artikel, waar jammer genoeg minder over gezegd wordt.
@breakingpoint: Het gehele onderdeel verwijderen helaas. Naast het feit dat koolstofvezel enorm duur is, kent het nog een nadeel. Het is zo goed als onmogelijk om te recyclen. Als ontwerper maak je de keuze of koolstofvezel geschikt is voor je product. Hierbij kijken we vooral naar de verwachte levensduur van een product en daarbij horende technische levensduur. Koolstofvezel is duurzaam wat betreft slijtagegevoeligheid maar niet bepaald duurzaam in een context van Greenpeace. Biodegradability is zo goed als nihil bij koolstofvezelcomposiet.
@AutomotiveDesigner: *verwachte
levensduurgebruiksduur van een product@AutomotiveDesigner: je hoort ook wel dat carbon fietskaders ‘moe’ worden, en gewoon breken na verloop van tijd. Zit dit er ook aan te komen met alle carbon monocoques die bij auto’s meer en meer gebruikt worden?
@breakingpoint: Ik ben niet bekend met fietskaders en de toegepaste composietmaterialen. Wat ik wel kan vertellen is dat alle materialen bekend zijn met moeheid. Echter het moment dat zichtbare plastische vervorming optreedt en moeheid dat vooraf is gegaan is van een (regulier) koolstofvezelcomposiet nauwelijks waar te nemen in een spanning/rek-diagram. Ik vermoed dus dat dergelijke fietskaders simpelweg zijn overbelast met krachten waarvan vooraf geen rekening is gehouden.
@breakingpoint: fietsen kunnen maar bepaalde krachten opvangen. Ze worden zo ontwikkelt om ideale langskrachten op de kunnen vangen, maar ze kunnen onwijs slecht tegen dwarskrachten. Ik doe zelf aan fietscross waarbij ik op een crossfiets rij van carbon, maar als je zo’n fietsje op z’n zijkant laat vallen (of je gaat op je plaat en fiets valt op de zijkant) dan kan er zomaar een scheur of een breuk in komen omdat ze niet gemaakt zijn voor dat soort krachten, evenals bij wielrenfietsen
@AutomotiveDesigner: Nogal wiedes, de koolstofvezel vergaat gewoon niet, omdat het een element is. Alleen kernfusie is sterk genoeg* om koolstof om te vormen in iets anders en dat gebeurt niet zo snel, kortom: alle koolstof die op aarde was, zal hier zijn en blijven.
Het feit dat het niet vergaat, betekent niet dat het slecht is voor het milieu.
Het plastic of hars is wel schadelijk voor het milieu, maar daar worden constant alternatieven voor gevonden.
* ok, de zwakke kernkracht ook.
Tof artikel.Alleen die McLaren met twee wielen zou kapotverboten moet worden!!!
@sydney: Waarom zou McLaren geen fiets mogen (laten) maken? Ferrari, Lamborghini, Audi, BMW, Volkswagen, zelfs Fiat doet het…
@Esprit_de_Flandre: Je bent op ‘Kans’ gekomen.Ga 4 topics terug.
@sydney: Huh?
Erg leuk en leerzaam artikel!
Leuk dat jullie steeds meer differentiatie in jullie artikelen aanbrengen!
Hoopt dat de jonkies nu weten dat het gewoon een plastic is met een paar extra vezeltjes.
@norge: yup
Altijd leuke weetjes
Eindelijk een artikel waar je iets van opsteekt !
Leuk artikel! Eindelijk weer iets echt inhoudelijks!
Mooi artikel, spoorde mij direct weer aan om op youtube.nl eens het geluid van de LFA te beluisteren:
https://www.youtube.com/watch?v=p6D7S2rcyIQ
Goed artikel, leuk om te lezen!
Een puntje alleen; de matte of glanzende afwerking ligt niet alleen aan droog of nat carbon maar ook aan de beschikbare mallen.
@FlighTom: Ja, daar schijn ik een beetje misgeschoten te hebben. Update geplaatst.
Dit is top, graag meer van dit soort posts!
Over de prijs: per kg is die fors hoger, maar volgens mij krijg je er een veel groter oppervlak voor terug dan staal.
Is dit dan wat het duurder maakt, of het gehele proces er omheen dat wellicht op handwerk aan komt?
@awesome: vooral het handwerk, de verhouding materiaal arbeid is vaak 70/30 bij metaal is het eerder 10/90
@jordyvn: andersom natuurlijk
@awesome: bij alu/staal heb je een dieptrekmal die per seconde een compleet spatbord kan vormen. Voor het lamineren van een spatbord ben je een halve dag bezig waarna de boel nog een aantal uren in de autoclaaf staat!
Uiteindelijk kom je dus op een product wat qua materiaalkosten ongeveer gelijk ligt maar vele malen arbeidsintensiever is.
@awesome: Een beetje prepreg kost zo’n 50 euro per vierkante meter, en kan oplopen tot enkele honderden euro’s voor de high-end prepregs. Daarnaast moet een lay-up uit meerder lagen bestaan om de stijfheid te verhogen, denk aan minimaal 4 a 5 lagen afhankelijk van de functie (esthetisch of functioneel), ook dit kan oplopen tot enkele tientallen of zelfs honderden lagen. Zo heb ik ooit eens zo’n draagvin voor een race-catamaran gezien welke ruim 5 centimeter dik was, puur opgebouwd uit laagjes CFRP. Ik stond toch aardig met mijn oren te klapperen toen ik dat zag.
Ben zelf meer thuis in de sandwichpanelen, dan voeg je een lichtgewicht kern toe aan de CFRP lay-up waarmee je de stijfheid van het paneel met tientallen procenten verhoogt terwijl het gewicht maar met enkele procenten omhoog gaat. Mooi spul om je goed in te verdiepen, komt stiekem aardig wat bij kijken.
Erg interresant artikel. Wat veel mensen niet weten is dat het Nederlandse bedrijf Fokker al jaren lange ervaring heeft met het werken met koolstof prepreg, maar ook met andere vezelversterkte kunstoffen zoals armide en kevlar.
Toyota/Lexus heeft een eigen weefmachine ontwikkeld om een eigen (volgens Toyo/Lexus superieure) weer te kunnen maken met nog meer stijfheid bijbgelijk gewicht… That’s commiment! En dan zijn er nog lieden die de Lfa te duur noemen….. Funny.
Leuk artikel, mis alleen het verschil tussen thermoharder en thermoplast. In de luchtvaart worden vooral thermoplasten gebruikt deze kun je bv. wel lassen !
@wybep: klopt, echter dit is erg specialist werk wat nog redelijk in de kinderschoenen staat. Wat men vaak vergeet is dat niet alleen het lamineren van prepreg een speciaal proces, het verspanen van composiet is ook erg lastig.
@wybep: thermoplasten maken langzaam een op mars. Voordelen zijn een snelle productie, hoge gebruikstemperatuur en de mogelijkheid tot lassen. Een belangrijk nadeel is dat er kruip in de hars kan zitten en dat de tooling een stuk duurder is dan thermoharders.
“BMW is de eerste massaproducent die (via zijn dochter SGL Carbon) koolstofvezel machinaal en… ”
Je bedoelt SGL ACF, een Amerikaanse JV tussen SGL Carbon en BMW. Groot verschil.
Interessant artikel. Als ik dit zo lees dan vind ik het best knap dat Alfa Romeo de 4C zo scherp kan aanbieden.
@moveyourmind: Dat is het zeker, dure engineering, hoge materiaal- productiekosten. Ik vind het knap.
Nu schijnt de rest van de auto redelijk plastic fantastic te zijn, dus daarmee hebben ze de prijs weten te drukken.
@moveyourmind: en dat terwijl de monocoque nog wel in Nederland is ontwikkeld. Bij TenCate.
Leuk artikel! Ik vind het altijd heel stoer om te melden dat mijn auto een carbon-composiet aandrijfas heeft, dat is best uniek geloof ik! 3 keer raden welke auto ik rijd!
Interessant artikel. Ik mis echter een paar kleine dingen:
Koolstofvezel is wel degelijk te recyclen. Het is niet goedkoop en het eindproduct is ook van iets mindere kwaliteit, maar nog steeds beter dan veel metaalcomposieten. Deze engelstalige website geeft daar veel meer informatie over:
http://www.adherent-tech.com/recycling_technologies/carbon_fiber_reclamation_faqs
“Metalen en plastics hebben gelijke eigenschappen in alle richtingen en zijn dus isotroop.” Het is eigenlijk andersom. Omdat ze isotroop zijn, hebben ze gelijke eigenschappen in alle richtingen. Het is echter zo dat metalen -waaronder veel staallegeringen- wel degelijk anisotroop kunnen zijn en dus richtingsgevoeligheid kunnen vertonen. Het productieproces is hierbij bepalend.
Het bepalen hoe vermoeiing werkt bij een specifiek stuk koolstofvezel is heel lastig. Bij metalen is dat een stuk simpeler en bij veel staallegeringen is het zelfs mogelijk het product ongevoelig te maken voor elastische vermoeiing (plastische vervormingen zijn weer een verhaal apart).
“Het is licht en kan tevens in voor metaal onmogelijke vormen gemaakt worden”
Volgens mij zijn metalen juist in veel meer vormen te maken. De bewerkingsmogelijkheden zijn simpelweg veel uitgebreider: draaien, frezen, gieten, lassen, 3D printen, smeden en vast nog wel andere bewerkingen waar ik niet aan heb gedacht. Daarnaast is het ook zo dat scherpe hoeken lastig te fabriceren zijn in koolstofvezel zonder extra langen of hars aan te brengen. Ook bij prepregs moet er goed worden gekeken naar de geometrie.
Nogmaals, goed artikel! Ik hoop dat er zo nog vele volgen.