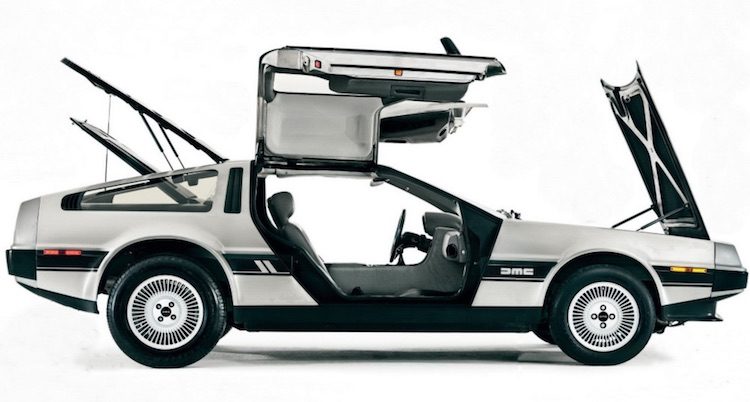
Staal dat terugslaat.
Als je het hebt over autoliefde dan denken de meesten waarschijnlijk aan sexy koetsen, gillende motoren en het geurige aroma van onverbrande benzine met een hint van olie uitgestoten door een patente klassieker op een koude herfstdag. Waar je waarschijnlijk niet direct aan denkt, is de vraag van welk materiaal het object van je affectie eigenlijk gemaakt is. Enige uitzonderingen daargelaten is dat namelijk vrij zouteloze, droge kost.
Dat wil niet zeggen dat het niet belangrijk is en dat er de laatste jaren veel ontwikkeling is geweest op dit vlak. We kennen allemaal de roestvrij stalen DeLorean en dankzij Jeremy Clarkson weet iedereen dat een Corvette ‘van plastic’ is. Maar ook voor huis-tuin-en-keuken auto’s wordt het gebruik van lichtgewicht materialen steeds belangrijker. Dit alles natuurlijk in verband met de uitstoot des doods.
In 2013 schreven we al dat aluminium de komende jaren steeds meer mainstream zou worden in de autowereld. Zoals altijd, hadden we gelijk. Aluminium heeft flink aan terrein gewonnen. Vroegah was staal goud, maar tegenwoordig bestaan auto’s gemiddeld voor tien procent uit alu en voor 55 procent uit staal. Doch staal laat dit niet op zich zitten en slaat keihard terug.
Grote staalmakers werken aan nieuwe legeringen die net zo sterk en vrijwel net zo licht als aluminium zijn, maar tegelijkertijd minder kosten. In 2021 moet het gaan gebeuren, volgens Automotive News. Fabrikanten zijn altijd op zoek naar puike deals en de staallobby hoopt dat investeringen in elektrische aandrijflijnen zoveel geld zullen opslokken dat autobedrijven interesse hebben om ’te beknibbelen’ op de rest van de auto. Zeker als de kwaliteit daar niet onder lijdt.
Zo blijkt wederom: hoe meer dingen veranderen, hoe meer ze hetzelfde blijven. Doe jij je Alu-commodities vast van de hand, of heb je balls of steel en zwicht je niet voor de mannen van staal?
Het is roestvast staal en geen roestvrij staal :-)
@joligejoffer: Het kan gewoon allebei.
@simonmc: en laat de RVS liggen in een zilte of basische omgeving en je zult zien dat ook RVS fantastisch kan roesten. Dan moet je weer uitwijken naar speciale nikkel-staal legeringen.
On topic: waar je in het bovenstaande artikel leest ‘de grote staalmakers’ moet je eigenlijk lezen ‘de westerse staalfabrikanten’. Want waar de concurrentie de laatste decennia in toenemende mate bestaat uit goedkoper staal uit China en/of India (die plat gezegd niet meer zijn dan schroot smelters), weten de Krupps en Corus/Tata’s van dit continent deze concurrentie vooral het hoofd te bieden door te innoveren op kwaliteit en vernieuwing. Dus moeten we met z’n allen maar hopen dat dit soort marktvernieuwing ook echt gaat voorzien in een passend alternatief of behoefte.
@RRRobert: RVS316 is prima toepasbaar in een zoute omgeving. Is niet voor niets voorgeschreven bij zoutproductielocaties van AkzoNobel…
@henrie: ik heb bijna tien jaar voor een toeleverancier voor olie- en gasindustrie gewerkt en als wij apparatuur in RVS 316 op een boorplatform installeerden, was het na twee jaar al zwaar aangetast. De enige reden dat dit vaak toch werd toegepast, was dat het goedkoper was om eens per twee jaar de apparatuur te vervangen i.p.v. het vier tot acht keer duurdere Hastelloy staal toe te passen.
@RRRobert: Dan is een boorplatform kennelijk toch nog een stuk zoutere omgeving dan een zoutfabriek. rvs 304 rot daar meteen weg. RVS 316 gaat vrij goed. Overigens wordt daar ook veel kunststof gebruikt, waar mogelijk. Zal ook niet zonder reden zijn…
@henrie: dat kan maar zo. Ik herinner me dat het ook vooral een combinatie is van zout + water + wind (= extreme erosie + corrosie). Plus het feit dat voor sommige toepassingen ook nog eens gloeiend hete stoom werd toegepast (RVS 304 en 316 kennen een behoorlijke sterkte afname bij temperaturen > 150°C en hoger). Er waren ook wel speciale verfsystemen die werden gebruikt om e.e.a. langer te beschermen, maar als vervanging erg lastig of kostbaar werd, koos men toch vaak voor Hastelloy (een merknaam voor nikkel-staal).
@joligejoffer: net als dat ik thuis een kast vol kogelvrije kleding heb ?
Ik ben benieuwd naar het lasproces of wordt het kitten om de boel vast te maken
@rob5nismo: er wordt een nieuwe manier uitgevonden om het te lassen. Nieuwe staal = nieuwe technieken
@moewat: daarom ben ik ook geïnteresseerd
@rob5nismo: Het zal wel gewoon puntlassen worden. Bijna alle staal kan je wel verhitten, pas als je materiaal toe gaat voegen kan het lastig worden.
@lekbak: want technisch gesproken is lijmen ook al lassen
@rob5nismo:
Nee dat is niet. Bij lassen gaat het om dezelfde grondstoffen bij elkaar te smelten. Bij lijmen komt er altijd een vreemde grondstof aan te pas.
Kijk nog maar eens goed in de schoolboeken hoe lassen beschreven wordt
@rob5nismo: “Lassen is het verbinden van materialen door druk en/of warmte, waarbij het materiaal op de verbindingsplaats in vloeibare of deegachtige toestand wordt gebracht (hoewel er ook uitzonderingen zijn, zie kouddruklassen), terwijl al of NIET materiaal met ongeveer dezelfde samenstelling wordt toegevoegd, waarbij continuïteit ontstaat tussen de te verbinden delen.” Dus…
@rob5nismo: heel veel auto’s bestaan voor grote delen uit lijm en speciale klinknagel verbindingen. Daar waar gelast wordt zijn het laserlassen. Maar dat is wel voornamelijk bij dure auto’s.
@transaxleman: klinknagels zijn van voor de oorlog, tegenwoordig is het een combinatie van lijm en puntlassen.
@transaxleman: Ik heb niet veel ervaring met ijzerwerk bij nieuwe auto’s maar ik kom zelden tot nooit een klink verbinding tegen. Lijmen en puntlassen eigenlijk vooral.
En wat gaan de kunststoffen van Ten Cate betekenen in de autoindustrie?
Nog lichter en sterker dan metaal, misschien is het probleem de energieabsorptie bij een botsing?
@kobus1967: ik denk dat het probleem zit in de fabricageprocessen. Staal en aluminium kun je volautomatisch walsen, persen, rekken en kanten in zo’n beetje elke denkbare vorm.
Kunststofvezels zul je altijd moeten vlechten tot matten, binden met hars, verbinden met lijm en vormen met de hand en/of mallen. Doordat dit zoveel arbeidsintensiever is, zie je deze techniek eigenlijk alleen maar bij de duurste prijsklassen (supercars en hypercars) en in enkele raceklassen.
@RRRobert: het vormen etc van composieten is niet zo’n punt volgens mij, het is vooral ook het ‘afbakken’ in een (dure) autoclaaf. Daarmee gewoon niet geschikt voor serieproductie. Een stalen plaatdeel is gewoon in 5 seconden klaar. Basta. Lakken en gaan…
Het leuke is dat deze legeringen veel in Europa gemaakt worden en maffe Trump zorgt ervoor dat dit voor Amerikaanse bouwers weer duurder wordt.
@porsche928: dus worden ze straks in Amerika gemaakt..
Voor zover ik weet is roesten het enige dat staal doet
“net zo sterk als alu” staal is sterker, gaat puur om betere corrosie weerstand en lager gewicht van alu.
@vtechlover: jaaaa maar er staat niet dát ze aan staal werken, maar aan een alternatief voor alu. Nuances ;)
“Grote staalmakers werken aan nieuwe legeringen die net zo sterk en vrijwel net zo licht als aluminium zijn, maar tegelijkertijd minder kosten.”
Uhm….. Kippengaas! Dat is licht!
Ontopic. Soortelijk gewicht van een stof wordt vooral bepaald door de plaats van het materiaal in het periodiek systeem. Ben reuze benieuwd met welke alchemie ze dit gaan verslaan.
Mogelijk wordt bedoeld dat door de sterkte van de legering er zo weinig van nodig is per M2 dat het een aluminium plaat met gelijke stijfheid kan verslaan?
Kom ik tóch weer uit op kippengaas!