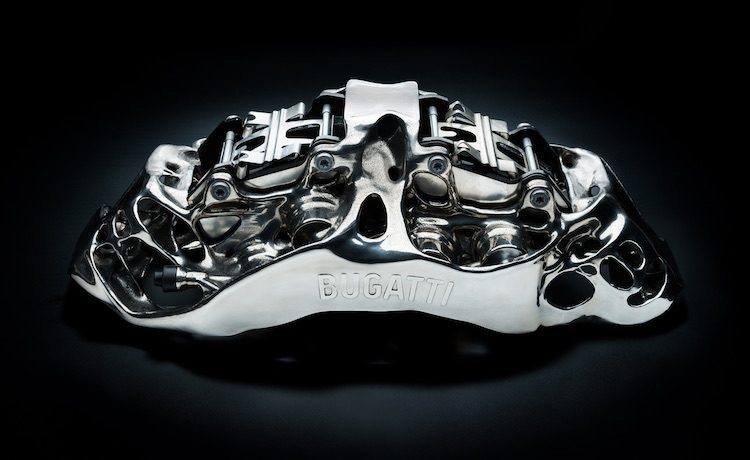
Dr. Claw is er niks bij.
Bugatti heeft weer een primeurtje te pakken. Je kijkt hier niet naar de grootste remklauw uit de autowereld. Maar dat is niet eens het punt: de klauw is tot stand gekomen door middel van 3D-printing, de heetste moderne technologie na Crispr en de Blockchain. Bovendien bestaat de unit niet uit het relatief zachte aluminium, maar uit het knoeperharde titanium. Daarmee is het volgens Bugatti ook meteen ’s werelds grootste functional component van titanium dat geproduceerd is met behulp van 3-D printing. Kortom, het is een bijzonder stukje techniek, dit bruut ogende stukje ho-ijzer (ho-titanium?).
Bugatti ontwierp de remklauw in samenwerking met een bedrijf uit Hamburg dat de epische naam Laser Zentrum Nord draagt. Je zou verwachten dat het wel wat voeten in aarde had om het essentiële onderdeel te ontwikkelen, maar Bugatti meldt trots dat het proces van idee tot product maar drie maanden in beslag heeft genomen.
Wat dat betreft is het wellicht een geruststellende gedachte voor bestaande Chiron-eigenaren dat hun 400 kilometer per uur snelle auto’s nog niet voorzien zijn van de nieuwe techniek. Voor toekomstige Chiron-eigenaren kan dat echter wel het geval zijn. Bugatti wil namelijk in de eerste helft van dit jaar al gaan testen met de nieuwe sterke en lichte klauwen.
Indrukwekkend. Lijkt wel alsof het als een bot gegroeit is.
@torsen: Misschien leuk om te vermelden.
Printen van één klauw duurt 45 uur en doet 2213 laagjes. Verder frezen en aanbrengen van schroefdraad kost nog eens 11 uur.
Gewicht van het ‘standaard’ exemplaar is 4,9 Kg t.o.v. 2,9 voor de titanium unit.
@torsen: Google maar eens op topology optimization, is mooi spul.
@silverarrow: 2kg per remklauw, petje af.
@silverarrow: inderdaad mooi spul. Benieuwd of we dat binnenkort vaker tegen gaan komen.
En uiteraard plakken ze er vervolgens een etiketje op waarop staat dat Cédric 350 manuren heeft besteed om deze remklauw handmatig met een diamantboortje te vervaardigen.
@berlinetta: Moeten ze toch eens met de PR afdeling gaan praten die dit persbericht naar buiten gebracht heeft. Straks raakt Cédric z’n baan nog kwijt.
Koenigsegg heeft ook de 3d Printing technologie gebruikt voor de turbo voor de 1:1. word tegenwoordig vaker gebruikt i.v.m lage kosten bij mindere volume.
@kimhung: En het einde van de uitlaat is ook geprint titanium.
@kimhung: ik heb me er toch vaak in vergist, dan geven ze aan 3D geprint … maar dan blijkt de mal 3D geprint te zijn en het onderdeel gegoten.
Fijn, staat je auto dalijk op kratjes, liggen de wielen ernaast maar hebben ze je klauwen geklauwd!
Tijdje terug al wat andere promotionele dingen voorbij zien komen van dit principe en technieken:
https://www.lightrider.apworks.de/en
http://www.apworks.de/
En wat dichter bij de auto`s:
http://www.apworks.de/blog/3i-print/
En zoals in de autoblog tekst ook al staat, moet het allemaal relatief eenvoudig zijn. Aanleveren van een bestaand onderdeel, en hun eigen programma berekendt alles opnieuw en komt met een nieuw (organisch) variant daarvan.
Erg vet, 3D printen is uitermate geschikt voor topology design vanwege de oneindige vormvrijheid. Gaan we veel meer zien in de toekomst.
“knoeperharde titanium”^^ Vergeleken met wat, aluminium?
Titanium gaat, als ik het me nog correct herinner, max tot 56 rockwell, hard, maar om nu te zeggen knoeperhard, dat is lichtjes overdreven… Het staal van je tafelmes is waarschijnlijk even hard of harder.